
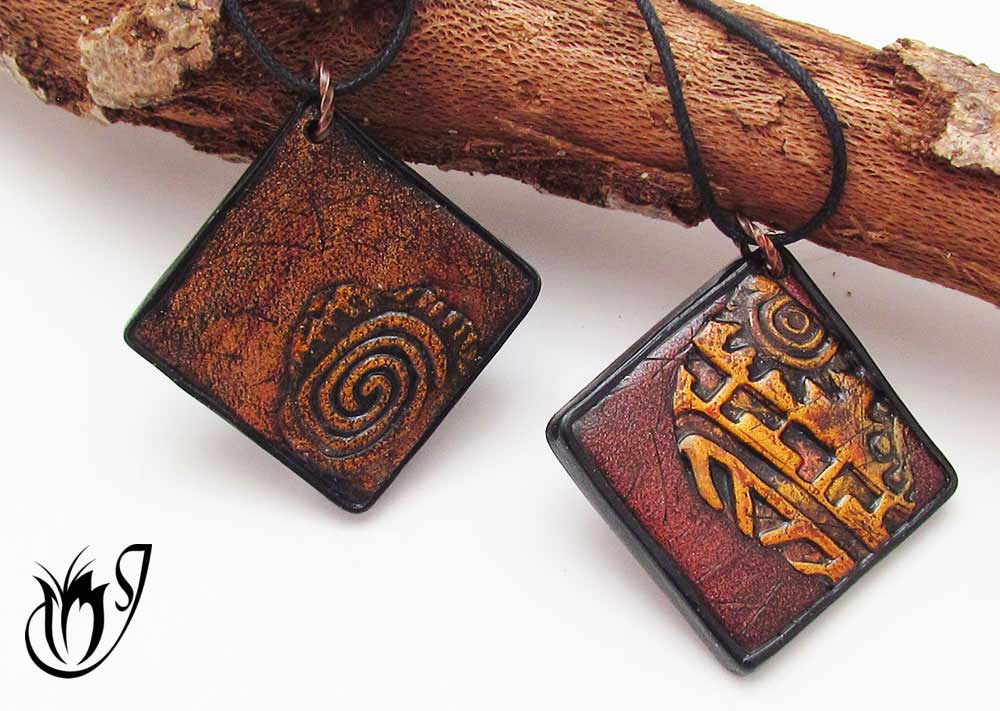
This means that you can use it to make dishes, utensils, and other kitchen items without worrying about whether they’re safe to use. One of the great things about oven-bake clay is that it’s food safe. I bought all these products myself and received nothing from the manufacturers.20 Kitchen Remodeling Ideas 2023 | Transform Your Space Today! It’s probably best to preheat to be sure of the oven temperature. What I’d conclude is that putting polymer clay in a cold oven and letting it gently heat up and cool down doesn’t seem to make a difference in plaquing, except possibly with Cernit. Some of the plaques near the surface caused bumps in the clay. Kato and Fimo plaqued regardless of method. I thought I might have better results if I conditioned it by hand, but it made no difference. I conditioned it with the pasta machine and when it baked, it had hundreds of tiny bubbles in it. This was my first time using Cernit and the clay I had was very soft. Wow!Ĭernit had no plaquing in the cold oven method, but had some in the preheated method. It came out of the oven with kind of a sticky film on it, so I rubbed that off with a paper towel and then buffed it. This time I conditioned it by hand before putting it through the pasta machine just to make a flat, uniform sheet. I’m so impressed that Pardo is almost transparent! I’ve only used it once before and found it very crumbly and difficult to condition.
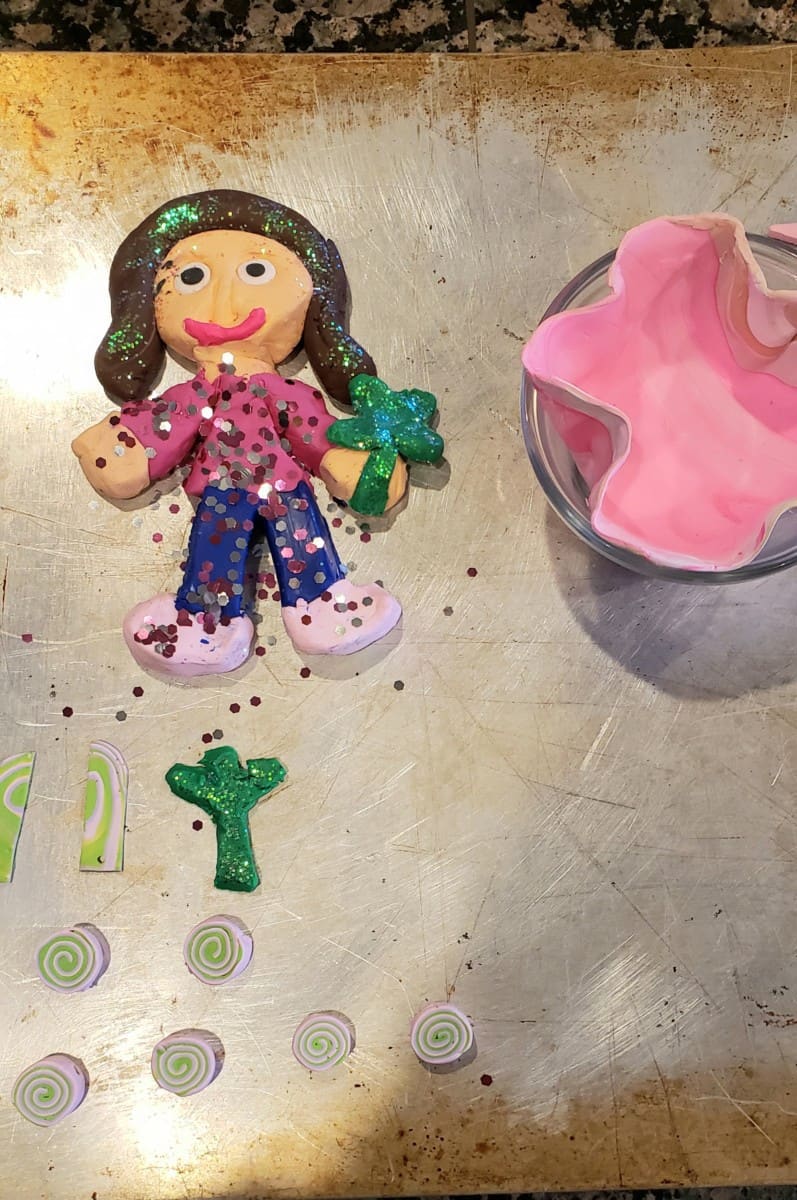
With Pardo, there was no plaquing with either method, just some very small bubbles that I probably made. The longer I baked Fimo, the more orange it got.
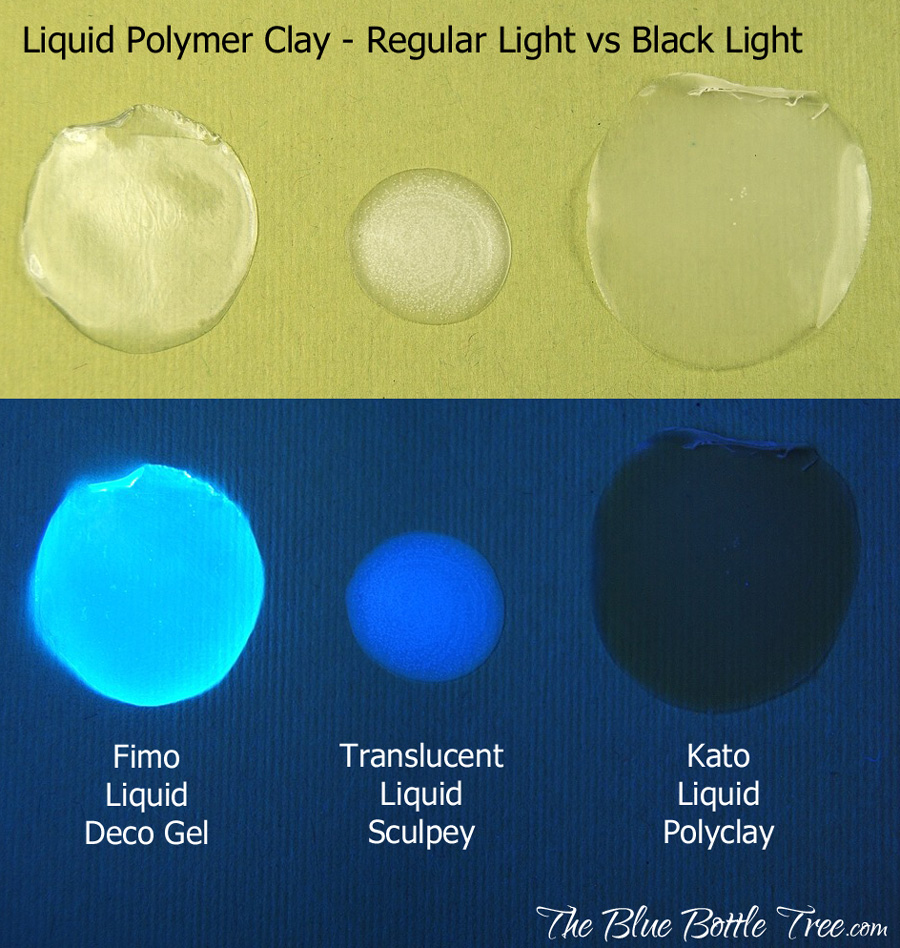
Thank goodness, because some of these look pretty bad. This test was to learn about preheating and plaquing, not to create nice-looking pieces of translucent polymer clay. Baked clays photographed on a lightbox to better show the plaquing. I gave 5 more minutes of baking time to those going into a cold oven.Īfter seeing the results, I decided to do two more tests using 20 and 45 minutes in the oven on the two clays that showed the most plaquing: Kato and Fimo. I followed the temperature recommendations for each and covered them with tin foil to bake for 30 minutes. I used five different brands: Fimo, Kato, Premo, Pardo and Cernit. I decided to test preheating versus a cold oven using translucent clay to see if it made any difference with plaquing. Hot clay is very pliable, so you have to be careful when taking it out of the oven, too. You have to be careful to not burn yourself when putting clay into a hot oven. The downside of preheating is you have to pay more attention. If you don’t meet those requirements, you can run into problems, such as crumbling and breaking.

Polymer clays need certain temperatures and durations to fuse. The benefit of preheating is that you know what the temperature is and can come closer to manufacturer’s recommendations. Plaquing happens in opaque clays, too, it’s just not as easy to see. It looks pretty bad unless you’re trying to make faux granite or jade. Plaquing is basically flat bubbles in the clay. The main reason I’ve been using this seemingly gentler method is because I read that it reduces plaquing. It does seems like less of a shock to the clay, but do I need to rethink? Unless I’m in a hurry, I’ve typically put polymer clay in a cold oven, baked it for 30 minutes and let it cool in the oven. Lovely, unbaked, translucent clays: Cernit, Pardo, Fimo, Kato and Premo.
